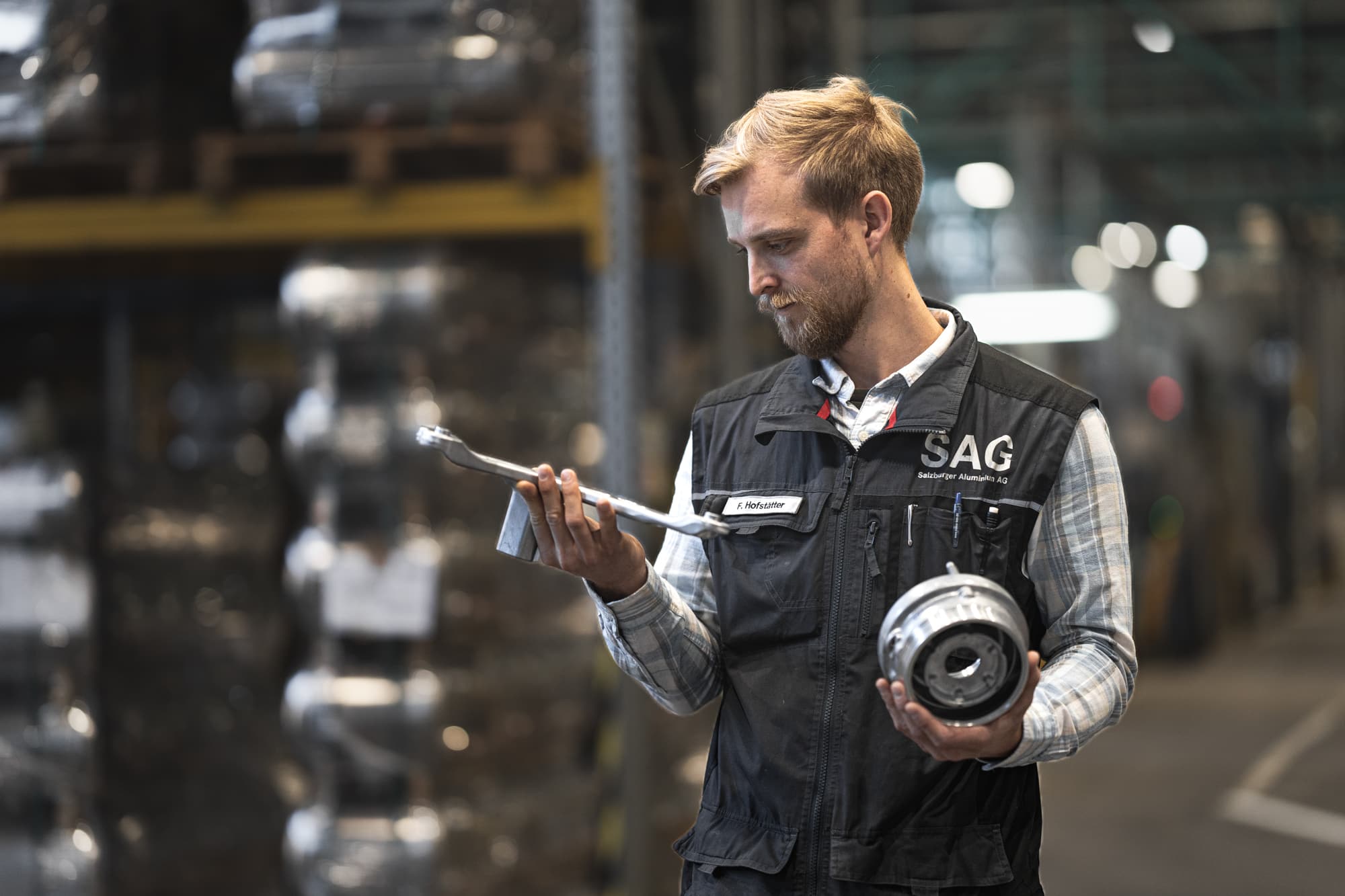
Prototyping
We develop, build and test prototypes to accelerate your product launch.
Challenges
Prototyping: turning ideas into real-world solutions
When developing a final product, a high-quality prototype is a crucial step in the process. A prototype allows companies to visualize and evaluate their concepts in a tangible and precise way. It offers a realistic and reliable preview of the end product.
At SAG, we use cutting-edge manufacturing technologies to produce prototypes that set the standard in quality and precision. This allows our clients to test, refine, and accelerate product development with confidence – bringing innovation one step closer to reality.

Smart, strong and ready to perform
Why choosing prototyping?
The starting point for SAG R&D could be installation space, boundary conditions or specifications. The R&D process leads to a virtually and physically tested prototype that is ready for use or further testing at the customer’s site. Also comprehensive real tests can be carried out in the well-equipped SAG laboratories.
- Test functionality and fit: Validate the exact fit and mechanical performance of your product early in the process. This enables design optimizations before moving into full-scale production.
- Achieve high precision: Joint development of material and components, delivers a level of detail and accuracy that is critical in industries such as aerospace, automotive, and medical technology.
- Refine designs faster: A physical prototype allows your team to quickly fine-tune the design. Even the smallest changes can be implemented without the cost or delay of tooling for mass production – saving both time and money.
Metal technologies
We offer numerous production techniques from our competence centers
Where precision meets performance
Innovative production process
At SAG, we are committed to the highest standards in prototype production. Our innovative process merges advanced technology with deep material expertise to deliver prototypes that are not only reliable but also rich in detail and functionality. Every step is designed to ensure top-tier quality and performance.
Our production process includes the following key stages:
- Design & Engineering: We begin with a detailed design phase in close collaboration with our clients. All prototype requirements are clearly defined, and our engineers ensure that every design is optimized for both aesthetics and performance.
- Precision Manufacturing: Using state-of-the-art machining and production techniques, we fabricate aluminium prototypes with exceptional accuracy. The result is a physical model that truly reflects the look and function of the final product.
- Testing & Evaluation: After production, the prototype undergoes thorough testing to verify performance, durability, and design integrity. This phase gives our clients the opportunity to review the prototype and request final adjustments—ensuring it meets every expectation before moving into full production.
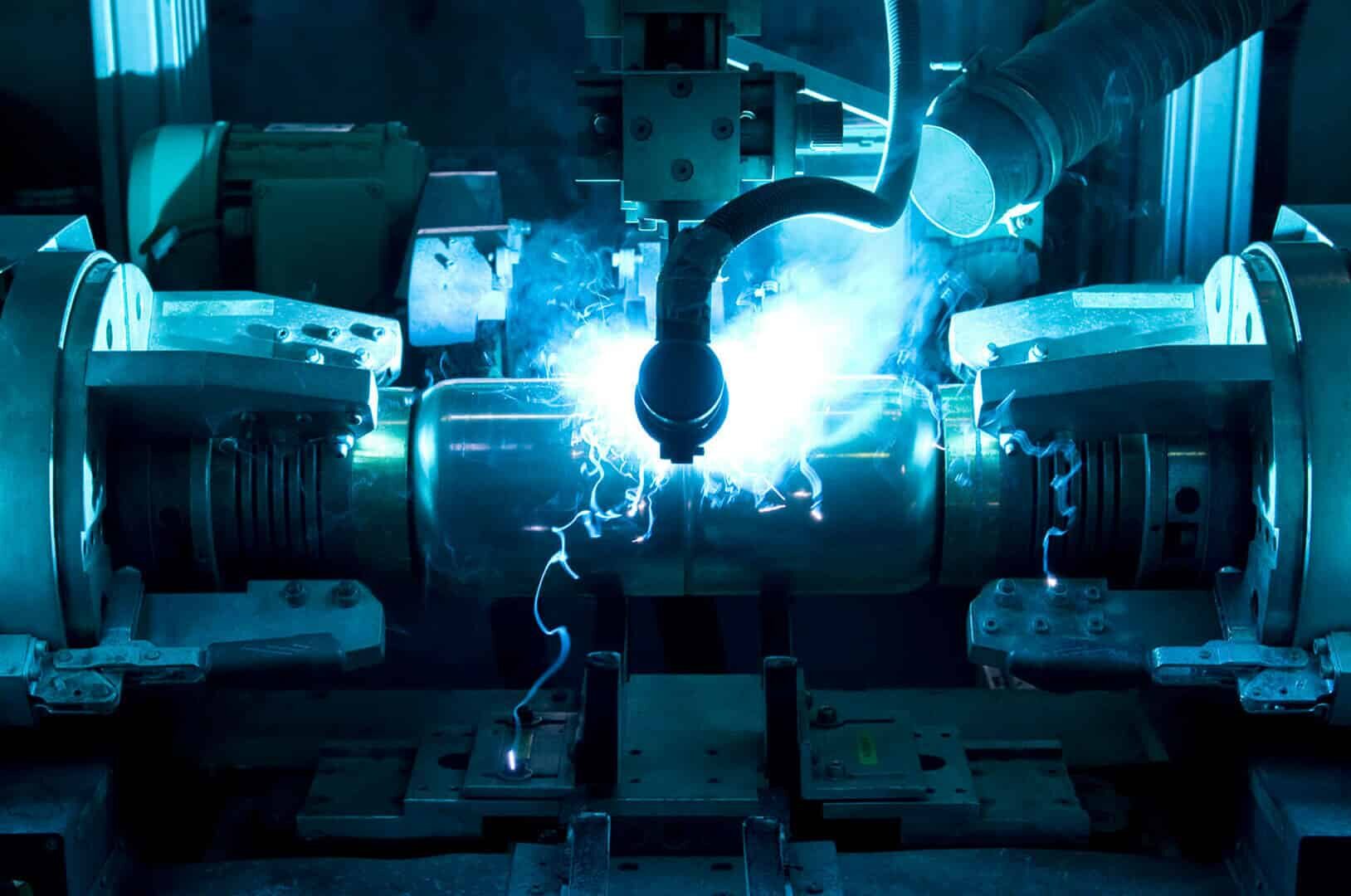

SAG GROUP